Ultra thin and ultra light, with outstanding optical performance, Active Matrix OLED displays have been a staple technology for smartphones and smaller consumer applications since around 2009. Happily, these small, powerful displays have recently grown in size, opening up opportunities for their use beyond handheld applications.
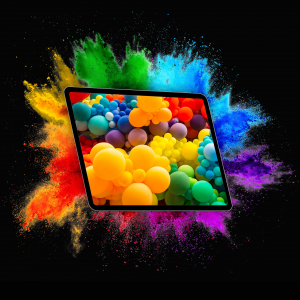
However, AMOLED comes with a word of caution: they are the most premium displays on the market and cost around four to five times the price of a regular display, so they’re certainly not appropriate for every application. But the difference is clear – it uses 80% less power, is around 2mm thick, and offers stunning optical quality. It’s the kind of display that can elevate a product.
The automotive and marine industries, for example, are beginning to adopt AMOLED, valuing it for its ultra-high contrast ratio (1,000,000:1), extensive and true color gamut, wide viewing and, of course, the thin, flexible design. It even withstands a wide temperature range, and now that AMOLED is available in sizes of 15.6” and larger, they will no doubt be found in the higher end of inflight entertainment and other luxury solutions which demand low power, but high quality displays, like powerful home automation applications.
But how does it differ from standard OLED? In the conventional OLED technology, the glass is sandwiched between two cathode layers. Inside these layers, there are two types of particles called electrons and holes. These particles move around when there’s an electrical charge applied. Electrons come from one side (the cathode), and holes come from the other side (the anode).
They meet in the middle, in another layer called the organic layer. When the electrons and holes collide in the organic layer and in the composite light-emitting layer, they emit excited molecules, which release energy in the form of light.
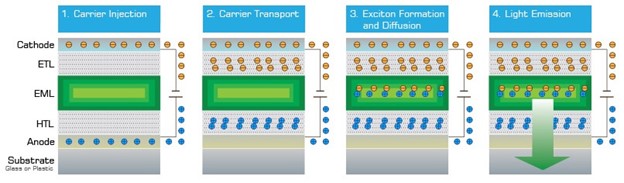
The luminous principle
Used with permission, © Everdisplay Optronics (Shanghai) Co., Ltd.
Today, there are two main types of OLED screens: passive (PMOLED) and active (AMOLED):
PMOLED screens are a simple structure, with each pixel represented by a separate cathode and anode control, but with no additional driver circuit. However, this structure restricts its use in high-resolution large screens.
AMOLED screens operate differently, with a drive circuit controlling the entire cathode surface and light emitting anode. This is how it uses less power while maintaining high-resolution, and fast response. Understandably, AMOLED gradually became the mainstream OLED display.
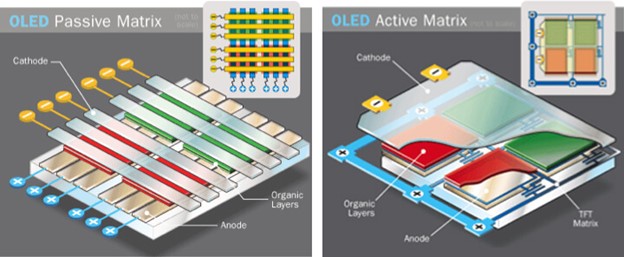
The driving Mode
Used with permission, © Everdisplay Optronics (Shanghai) Co., Ltd.
In high-resolution AMOLED, the size of the driving circuit has become increasingly smaller and smaller, while the electrical performance requirements have become more sophisticated. Conventional Si (Amorphous Silicon, A-Si) technology has struggled to meet these requirements, so Low-Temperature Polysilicon (LTPS) is the technical solution to this problem. Amorphous silicon can be transformed into polysilicon, which has higher carrier mobility and lower defect density.
If you feel that your application would be a perfect match for AMOLED, please get in touch with our experts, who have 15.6” demo units available to try. Of course, our display experts at Avnet can advise you on the best possible display solutions for your project – even if AMOLED isn’t quite what you require.
Find out how Avnet Embedded can propel your product innovation and get in touch today.
Talk to the experts!
Let us know about your product or your challenge and our team will get in touch to discuss how we can help.